Table of Contents
ToggleLaser Welding
Optimized & Industry-ready Solutions
For All Your Complicated Needs
Laser welding:
Lasers provide contact-free, high-speed metal welding solutions for advanced manufacturing across countless industries.
With Bluewo fiber lasers, laser welding has become a highly reliable, easily automated process that provides the highest part quality, typically at the lowest processing costs, and virtually maintenance free.
High speed laser welding produces high part yields at low operating costs that results in the lowest cost-per-part:
1. High-precision accuracy for joining even small parts
2. Low heat input for minimal distortion
3. Non-contact welding – no degradation in welding quality
4. No current passes through the part
5. Weld dissimilar metals (e.g. Cu to Al)
6. Minimal maintenance – high tool availability
7. Easily automated for high-productivity, high-yield manufacturing
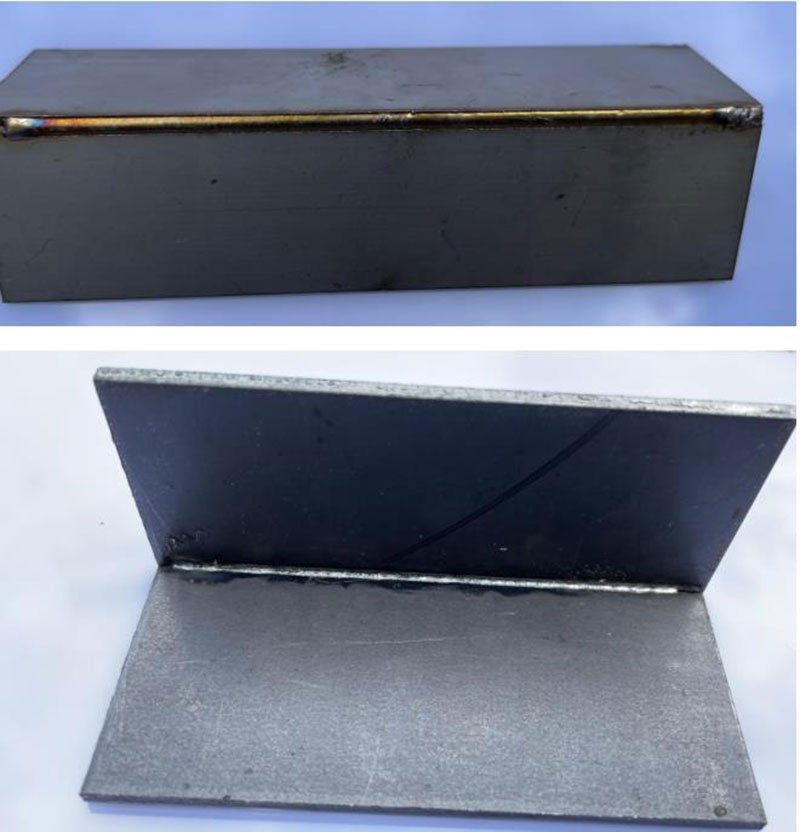
Laser Welding FAQ
Laser welding is a process used to join together metals or thermoplastics using a laser beam to form a weld. Being such a concentrated heat source, in thin materials laser welding can be carried out at high welding speeds of metres per minute, and in thicker materials can produce narrow, deep welds between square-edged parts.
Laser welding machine consists of laser oscillator, optical path, laser focusing parts, driving parts and protective gas system. The laser beam oscillated by the oscillator is introduced into the focusing optical system through the optical path.
Laser welding operates in two fundamentally different modes: conduction limited welding and keyhole welding. The mode in which the laser beam will interact with the material it is welding will depend on the power density across the beam hitting the workpiece.
Laser welding can be used to join a wide range of materials, including structural steel, alloy steel, low-alloy steel, carbon steel, duplex, aluminum, copper, titanium, nickel, magnesium, refractory metals and chemically active metals. Laser welding also enables unusual connections, such as aluminum to aluminum.
Laser precision allows for better quality welds, faster throughput, reduced post-processing costs and access to new domains of application. The main drawback of laser welding is the hefty price tag for the equipment.
The most widely used shielding gases for laser welding of steels are helium and argon. Helium produces significantly more penetration than argon in penetration‐mode laser beam welding. Another gas that has been proposed as an alternative to these inert gases is carbon dioxide.
The thinnest sheets of stainless can also be laser welded due to this optimal control. Reduced Thermal Distortion: An additional benefit from laser welding stainless steel is reduced thermal distortion and residual stresses when compared to conventional welding techniques
- Titanium and steel.
- Aluminum and copper.
- Aluminum and stainless steel.
- Aluminum and carbon steel.
Laser rust removal, a type of laser cleaning, is an effective process for cleaning up metal parts. Using a fiber laser cleaning system, rust and other contaminants can be quickly and completely removed without damaging the metal underneath.
Fiber Laser Features
Why are more manufacturers switching to welding with fiber lasers from traditional welding techniques?
Staying competitive today requires cost reductions, efficiency gains, and repeatable part quality that cannot be met by traditional techniques that rely on increasingly scarce, highly-skilled craftsmen. Enabled by unprecedented no-maintenance, high-reliability, and low-cost IPG fiber lasers, laser welding systems have become the preferred welding solution for the manufacturing industry.
Gas Metal Arc Welding (GMAW) VS Fiber Laser Welding
GMAW or MIG is a traditional technique using a consumable electrode that works well for larger, badly fitting parts.
Fiber laser welding does not use consumable electrodes, requires less edge preparation, is easily automated, and is up to 5x faster. Fiber lasers also provide more precision and lower heat input.
Plasma Arc Welding (PAW) VS Fiber Laser Welding
PAW is faster than GTAW, but much slower than laser welding. Having a large melt pool, PAW is good for badly aligned parts, but creates too much heat for many applications.
Fiber lasers offer higher precision, are faster, and have lower heat input in a non-contact process. Laser Wobble Welding is as effective on misaligned parts and does not require daily maintenance of the process head.
Gas Tungsten Arc Welding (GTAW) VS Fiber Laser Welding
GTAW or TIG uses a non-consumable electrode and provides better process control than GMAW but any filler has to be added separately.
Fiber lasers are up to 10x faster with higher precision, lower heat input, and are more easily automated.
Resistance Spot Welding (RSW) VS Fiber Laser Welding
RSW is typically used for joining two pieces of material that are stacked on top of each other.
Fiber lasers only need single-side access, are much faster, and produce higher-strength welds. Fiber lasers do not require electrodes and eliminate the costs and time for electrode replacement.
Electron Beam Welding (EB) VS Fiber Laser Welding
EB welding provides excellent weld quality and a low heat-affected zone. Because the process is in a vacuum chamber, contaminant levels are very low.
Fiber laser welding speed is similar to the electron beam, but because lasers do not require part transfer through a vacuum chamber, laser cycle time is dramatically shorter.