Table of Contents
ToggleLaser Cutting
Optimized & Industry-ready Solutions
For All Your Complicated Needs
Laser Cutting:
The high precision, high speed, and quality of laser cutting have made it the technology of choice for advanced manufacturing across countless industries. With BLUEWO fiber lasers, laser cutting has become a reliable and highly cost-effective solution, resulting in increased adoption throughout the metal manufacturing world.
Benefits of fiber laser cutting include:
1. Precise and repeatable high-quality cuts
2. High-speed cutting
3. Non-contact cutting – no degradation in cut quality
4. Minimal maintenance – high tool availability
5. Variety of lasers to cut non-metallic materials
6. The scalable process from micro-cutting stents up to shaping structural steel
7. Easily automated for maximum productivity
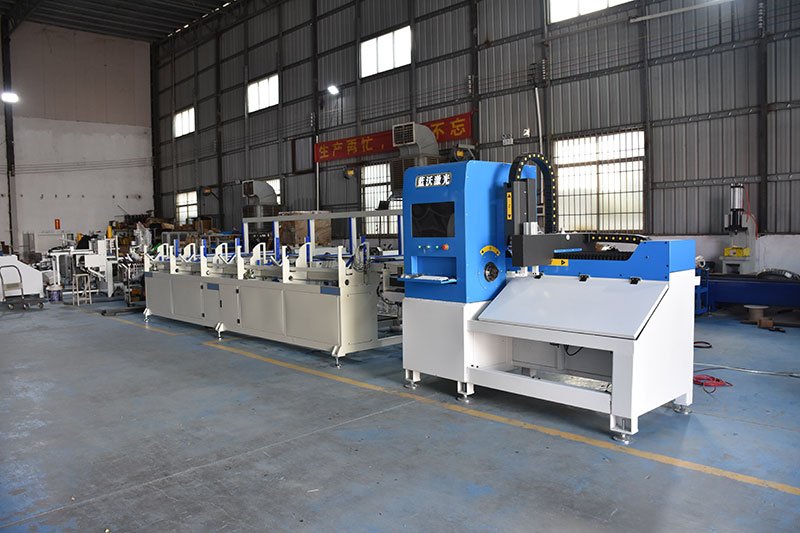
Fiber lasers FAQ
A fiber laser is a type of laser that uses optical fibers as the active gain medium, instead of traditional solid-state laser materials such as crystals or glasses.
In a fiber laser, a doped fiber, usually made of silica glass, is pumped with high-intensity light from a semiconductor laser or another fiber laser. The doping material, usually a rare earth element such as erbium, ytterbium, or neodymium, gives the fiber its optical gain properties.
As the pumping light passes through the fiber, it stimulates the emission of photons by the doping atoms, creating a population inversion and amplifying the light signal. The amplified light is then reflected back and forth inside the fiber, creating a laser beam that exits the fiber through one or both ends.
Fiber lasers are known for their high efficiency, compact size, and excellent beam quality, making them suitable for a wide range of industrial and scientific applications, including material processing, communication, medical devices, and scientific research.
Fiber lasers use pump light from what is called laser diodes. These diodes emit light that is sent into the fiber-optic cable. Optical components located in the cable are then used to generate a specific wavelength and amplify it. Finally, the resulting laser beam is shaped and released.
With recent breakthroughs, fiber lasers provide high quality cuts with thicker materials. Fiber lasers also cut thinner materials faster than CO2 and are superior in cutting reflective metals, which provides a much lower cost of ownership. 10 advantages of fiber laser machine
Fiber lasers are everywhere in the modern world. Due to the different wavelengths they can generate, they are widely used in industrial environments to perform cutting, marking, welding, cleaning, texturing, drilling and a lot more. They are also used in other fields such as telecommunication and medicine.
Fiber lasers can process mild steel, stainless steel, titanium, iron and nickel as well as reflective metals such as aluminum, brass, copper and precious metals (silver and gold). They also work well with materials that have anodized and painted surfaces.
In fact, the diode module in a fiber laser typically last three times longer than other technologies. Most lasers have a life of around 30,000 hours, which typically equates to about 15 years’ use. Fiber lasers have an expected life of around 100,000 hours, which means about 45 years’ use.
The maintenance requirements for fiber lasers can vary depending on the specific model and usage conditions. In general, however, fiber lasers are known for their low maintenance needs compared to other types of lasers.
One reason for this is that fiber lasers have fewer moving parts than other types of lasers, such as gas or solid-state lasers. This means there are fewer parts that can wear out or break over time.
Additionally, fiber lasers typically have a longer service life than other types of lasers. Many manufacturers estimate the lifespan of their fiber lasers to be upwards of 100,000 hours.
That being said, regular maintenance can still be necessary to ensure optimal performance and prevent any issues from arising. Some common maintenance tasks for fiber lasers include cleaning the lenses and mirrors, replacing worn parts, and checking the alignment of the laser beam.
The frequency of these maintenance tasks will depend on factors such as the intensity and duration of usage, the environment in which the laser operates, and the specific model of the fiber laser. It is always best to consult the manufacturer’s guidelines for recommended maintenance intervals.
Prices and costs of laser cutting machines fluctuate greatly depending on the design, type, and ability of laser. If you plan to cut metal, tough woods, or other dense materials, you’ll need a higher watt laser than in case you wished to cut thinner materials, like cloth. On the other hand, the more complex the laser’s wattage, the higher the cost. It’s your choice to balance price and practicality.
The power of a fiber laser can have a significant impact on its performance in various ways. Some of the key ways in which power affects the performance of a fiber laser are:
Cutting and Welding Capability: Higher power fiber lasers are capable of cutting thicker and tougher materials than lower power lasers. They can also weld thicker and more complex materials with greater speed and accuracy. This makes them ideal for use in industrial manufacturing applications where high precision and speed are crucial.
Marking and Engraving: Fiber lasers with higher power can create deeper and more permanent marks on a wider range of materials than lower power lasers. This is important in industries such as jewelry making, where intricate designs need to be engraved onto metals and other hard surfaces.
Efficiency: Higher power fiber lasers can be more efficient in terms of their energy consumption and operational costs. They require less maintenance and can produce higher output with less waste.
Cost: As the power of a fiber laser increases, so does the cost of the laser itself, as well as the cost of running and maintaining it. This means that higher power lasers may not be cost-effective for certain applications, especially those that don’t require high levels of precision or speed.
Overall, the power of a fiber laser is an important factor to consider when selecting a laser for a particular application. It is important to choose a laser with the appropriate power level that can meet the specific needs and requirements of the application in question.
The main difference that determines the type of materials each laser can process is the wavelength. A fiber laser usually has a wavelength of 1,060 nm while CO2 lasers have wavelengths in the 10,600 nm range. In general, fiber lasers have many advantages over CO2 lasers.
The wavelength of fiber laser is only suitable for laser cutting or engraving metal workpieces, which makes its area of application very limited. On the other hand, Diode lasers can cut or engrave a variety of materials like acrylic, wood, plastics, fabrics, leather, aluminum, etc.
A pulsed laser produces a series of pulses at a certain pulse width and frequency until stopped. Continuous wave (CW) simply means that the laser remains on continuously until stopped.
Fiber laser beams can be used to cut, weld, engrave, and clean certain materials (usually metals).
Generally, when laser cutting metals with fiber lasers, the upper limit on thickness of the metal sheet to be cut is around 20 – 25 mm for mild steels. Above this thickness, higher power CO2 lasers are used but with specialized fiber lasers for a higher price, it is possible to cut thicker plates than this.
The key differentiating factor is thickness range and cut quality. Plasma machines can only cut conductive materials. Fiber laser machines are also limited to metals (the 1.06 μm wavelength of a fiber laser cannot be absorbed by non-metals).
The wavelength of a fiber laser can have a significant impact on its performance, as it determines the laser’s ability to interact with different materials and to deliver specific amounts of energy to a target.
Here are a few ways in which the wavelength of a fiber laser can affect its performance:
Absorption by the material: The absorption of laser energy by a material depends on the wavelength of the laser. Different materials absorb light energy differently at different wavelengths. For example, metals typically absorb laser energy more efficiently at shorter wavelengths, while polymers and other organic materials may absorb more efficiently at longer wavelengths. Therefore, the choice of laser wavelength can affect the efficiency of laser-material interactions.
Precision and accuracy of cuts: The wavelength of a fiber laser can also affect the precision and accuracy of cuts made by the laser. This is because the size of the laser spot and the depth of the cut depend on the laser wavelength. In general, shorter wavelengths are associated with smaller laser spots, which can lead to higher precision and accuracy in cutting.
Fiber optic properties: The properties of the fiber optic material used in the laser can also be affected by the laser wavelength. Some fibers have greater attenuation (i.e., they lose more energy) at certain wavelengths, which can impact the laser’s output power and stability.
Heat dissipation: The wavelength of a fiber laser can also affect the amount of heat generated during operation. Shorter wavelengths generally produce more heat than longer wavelengths, which can impact the laser’s lifespan and reliability.
Overall, the choice of laser wavelength will depend on the specific application and the material being processed. In general, a fiber laser with a broader wavelength range may be more versatile, as it can be used for a wider range of materials and applications.
The beam quality of a fiber laser has a significant impact on its performance. Beam quality refers to the ability of a laser beam to maintain its focus over distance and is typically measured using a parameter called the M² factor.
In general, a fiber laser with good beam quality will have a small M² factor, which indicates that the laser beam can be focused to a small spot size over a relatively long distance. This makes the laser useful for applications that require high precision and accuracy, such as laser cutting and welding.
On the other hand, a fiber laser with poor beam quality will have a larger M² factor, which means that the laser beam diverges more quickly and cannot be focused to a small spot size over a long distance. This limits the usefulness of the laser for applications that require high precision and accuracy.
In addition to affecting the laser’s ability to focus, the beam quality of a fiber laser can also impact its power output and efficiency. A laser with good beam quality will typically have higher power output and efficiency than a laser with poor beam quality, since it can more effectively convert input power into laser light.
Overall, the beam quality of a fiber laser is a crucial factor that can significantly impact its performance, making it important to carefully consider when selecting a laser for a particular application.
Fiber lasers are powerful and potentially hazardous devices that can cause serious injury if not used properly. Here are some safety precautions that should be taken when operating a fiber laser:
1.Personal protective equipment: Always wear appropriate personal protective equipment (PPE) such as safety glasses or goggles that are designed to protect against the specific wavelength of the laser being used. It is important to ensure that the PPE provides adequate protection, is in good condition, and fits properly.
2.Controlled access: Restrict access to the laser area to authorized personnel only. Install warning signs and barriers to prevent unauthorized access.
3.Proper ventilation: Ensure proper ventilation of the laser area to prevent the accumulation of hazardous fumes or dusts generated by the laser process.
4.Safe laser operation: Follow the manufacturer’s instructions for operating the laser and ensure that it is set up properly. Do not modify or tamper with the laser in any way.
5.Emergency shutdown: Have an emergency shutdown procedure in place and ensure that all personnel are trained in its use. This should include procedures for power failure, fire, and other emergencies.
6.Laser curtains: Use laser curtains to prevent laser light from escaping the laser work area and potentially causing harm to personnel.
7.Fire safety: Have fire extinguishers, fire alarms, and smoke detectors in place and ensure that all personnel are trained in their use.
8.Maintenance and inspection: Regularly inspect the laser and its components for signs of damage or wear, and perform any necessary maintenance as recommended by the manufacturer.
Overall, it is important to be aware of the potential hazards associated with fiber lasers and take appropriate safety precautions to ensure safe operation.
Fiber Laser Features
Why are more manufacturers turning to cutting with fiber lasers as opposed to traditional and more conventional methods?
CO2 Laser Cutting VS Fiber Laser Cutting
CO2 lasers provide smooth cutting edges for some thicker materials (>25 mm)
With recent breakthroughs, fiber lasers provide high quality cuts with thicker materials. Fiber lasers also cut thinner materials faster than CO2 and are superior in cutting reflective metals, which provides a much lower cost of ownership.
Waterjet Cutting VS Fiber Laser Cutting
Waterjet cutting is effective for cutting extremely thick materials (>25 mm)
In all other cases, fiber lasers provide higher throughput, more consistent quality and decreased downtime compared to waterjets.
Plasma Cutting VS Fiber Laser Cutting
Plasma cutting equipment is among the cheapest alternatives to choose from in the market.
Fiber cutting has lower consumables cost. Cutting with fiber lasers improves cut precision, quality and production yield, providing superior parts at lower prices
EDM Cutting VS Fiber Laser Cutting
Electrical discharge machine cutting provides excellent accuracy and minimal heat damage to materials.
Fiber lasers offer comparable precision AND are up to 10x faster than EDM cutting – delivering much higher output and productivity.