Table of Contents
ToggleLaser Cleaning
Optimized & Industry-ready Solutions
For All Your Complicated Needs
Laser Cleaning:
Lasers can provide high-speed cleaning and surface preparation in virtually all industries. The low-maintenance, easily automated process can be used to remove oil and grease, strip paint or coatings, or modify surface texture, for example adding roughness to increase adhesion.
Benefits of fiber laser cleaning include:
1. No abrasive materials are used, with no problems of contaminant separation and disposal
2. No solvents are used – chemical-free and environmentally friendly process
3. Spatially selective – cleaning only the area required, saving time and costs by ignoring regions that don’t matter
4. Non-contact process never degrades in quality
5. Easily automated process that can lower operating costs by eliminating labor while giving greater consistency in results
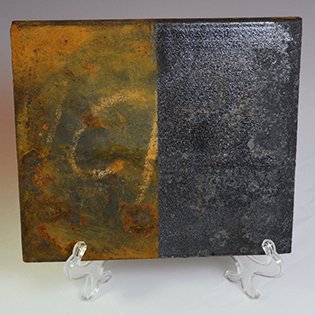
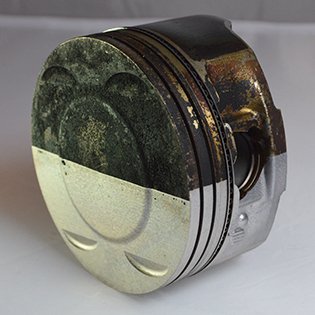
Laser Cleaning FAQ
Laser cleaning technology works by sending nanosecond-length pulses of laser light towards a surface. When it interacts with contaminants that absorb laser light, the contaminants or coating particles will either turn into a gas or the pressure of the interaction will cause particles to free from the surface.
Laser cleaning is a non-contact surface cleaning technology that uses a high-energy laser beam to remove contaminants or unwanted layers from a surface. The efficiency and effectiveness of laser cleaning can be influenced by various factors, including:
1. Laser wavelength: The wavelength of the laser determines the absorption characteristics of the material being cleaned. The laser wavelength should be selected based on the absorption spectrum of the material to ensure efficient cleaning.
2. Laser power: The power of the laser affects the amount of energy delivered to the surface being cleaned, which can influence the rate and effectiveness of cleaning.
3. Laser pulse duration: The duration of the laser pulse can affect the amount of material removed from the surface. Shorter pulses are typically more effective for cleaning delicate materials, while longer pulses are better for more robust materials.
4. Laser spot size: The size of the laser spot can influence the cleaning efficiency and the precision of the cleaning process. A smaller spot size can provide higher precision but may require longer cleaning times.
5. Scanning speed: The scanning speed of the laser beam over the surface being cleaned can affect the cleaning efficiency. A slower scanning speed can provide better cleaning but may increase the overall cleaning time.
6. Surface characteristics: The surface properties, such as roughness, reflectivity, and hardness, can affect the efficiency and effectiveness of laser cleaning. Materials with higher reflectivity may require higher laser power to achieve effective cleaning.
7. Contaminant type and thickness: The type and thickness of the contaminant being removed can affect the laser cleaning process. Some contaminants may require higher laser power or longer cleaning times to be effectively removed.
8. Environmental factors: Environmental factors, such as temperature and humidity, can also affect the efficiency and effectiveness of laser cleaning. Higher temperatures can increase the evaporation rate of contaminants, while higher humidity can affect the laser beam’s absorption characteristics.
9. Laser cleaning system setup: The configuration of the laser cleaning system can also affect the efficiency and effectiveness of the process. Factors such as the distance between the laser and the surface, the angle of incidence, and the focal length can all impact the cleaning efficiency.
1. General size, area, and geometry of the parts needing to be cleaned
2. Material substrate(s)
3. Coating/contaminant type and thickness
4. Current cleaning type, rate, and cycle
5. Desired cleaning rate
6. Previous processing steps in the part lifecycle
7. Next steps after cleaning
8. Operational details surrounding the laser process
Laser beam cleaning offers high precision and reproducibility, therefore saving enormous costs in industrial series production. The investment in current laser technology is often many times cheaper than that in, for example, wet chemical alternatives.
Laser technology works best for small, targeted areas, so larger surface areas can take longer to clean and may not produce desired results. Laser cleaning is also restricted when cleaning crevices — such as the inside of pipes.
Laser cleaning is effective in removing corrosion from production lines with metallic materials. Focused fiber laser on a metal surface can efficiently remove impurities from a material without damaging the substrate. It is a contactless process, safe and very versatile.
Fiber Laser Features
Why are more manufacturers using laser cleaning for material preparation?
Laser cleaning offers multiple advantages over traditional approaches. It does not involve solvents and there is no abrasive material to be handled and disposed of. Compared with other processes that are less detailed, and frequently manual processes, laser cleaning is controllable and can be applied only to specific areas of a part, can be easily automated to maximize productivity, and provides the guaranteed repeatability demanded by an increasing number of quality standards.
Abrasive Blasting VS Fiber Laser Cleaning
While the cleaning is easy and effective, the cost lies in the collection and disposal of the blast media, which often has to be separated from the paint debris, which has its own treatment issues.
Fiber lasers eliminate the blast media problem. They provide a more controlled process that does not accidentally damage a surface through excessive removal, and can also be used on thin and composite materials that would be damaged by the particle impact. Fiber laser cleaning is always consistent, independent of operator effects, and can scale to suit the job size by a selection of the laser power.
Chemical Cleaning VS Fiber Laser Cleaning
Good for cleaning surface contamination from a whole part, chemical cleaning is not easily applied to a selective area. Disposing of the chemicals is an increasingly difficult and costly challenge due to regulatory controls.
Fiber lasers can be applied selectively. With no chemicals to degrade, quality is consistent, and there are no chemical solvent disposal issues. With no drying time, parts are available immediately.
Cold Jetting VS Fiber Laser Cleaning
Also known as dry ice blasting, cold jetting has similar characteristics to abrasive blasting, but without the problems of abrasive material recovery and disposal.
Fiber laser cleaning has little risk of operator hearing damage, has no special ventilation requirements, and is more easily controlled when dealing with small parts.
Thermal Cleaning VS Fiber Laser Cleaning
Thermal cleaning is often used for removing organic contaminants such as polymers and plastics, often with excessive heat necessary for the application.
Laser cleaning is dramatically faster. It can remove a wider range of materials, including metals and the temperature of the part remains lower, with less chance of cracking or distortion. Laser cleaning is more energy efficient, and parts are immediately available.
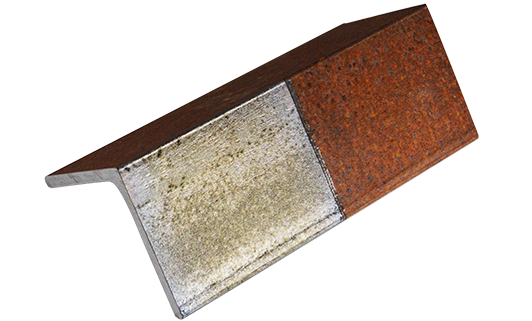